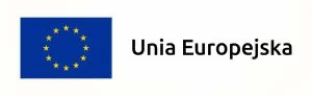
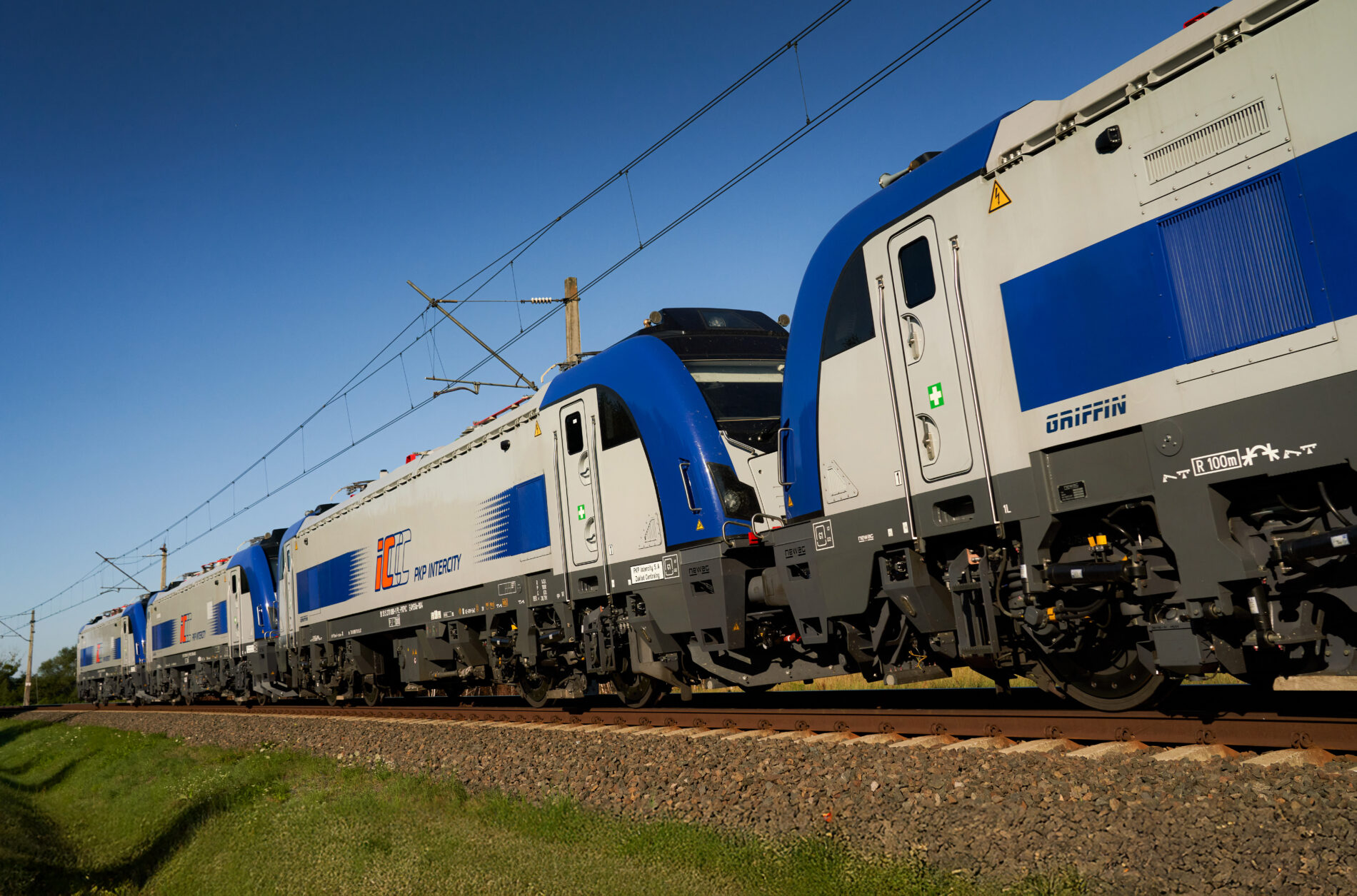
Przyszłość nabiera tempa
Oferta
Produkty, które gwarantują komfort, bezpieczeństwo i efektywność transportu. Zaufaj doświadczeniu, które kształtuje przyszłość kolei.
Platforma Impuls
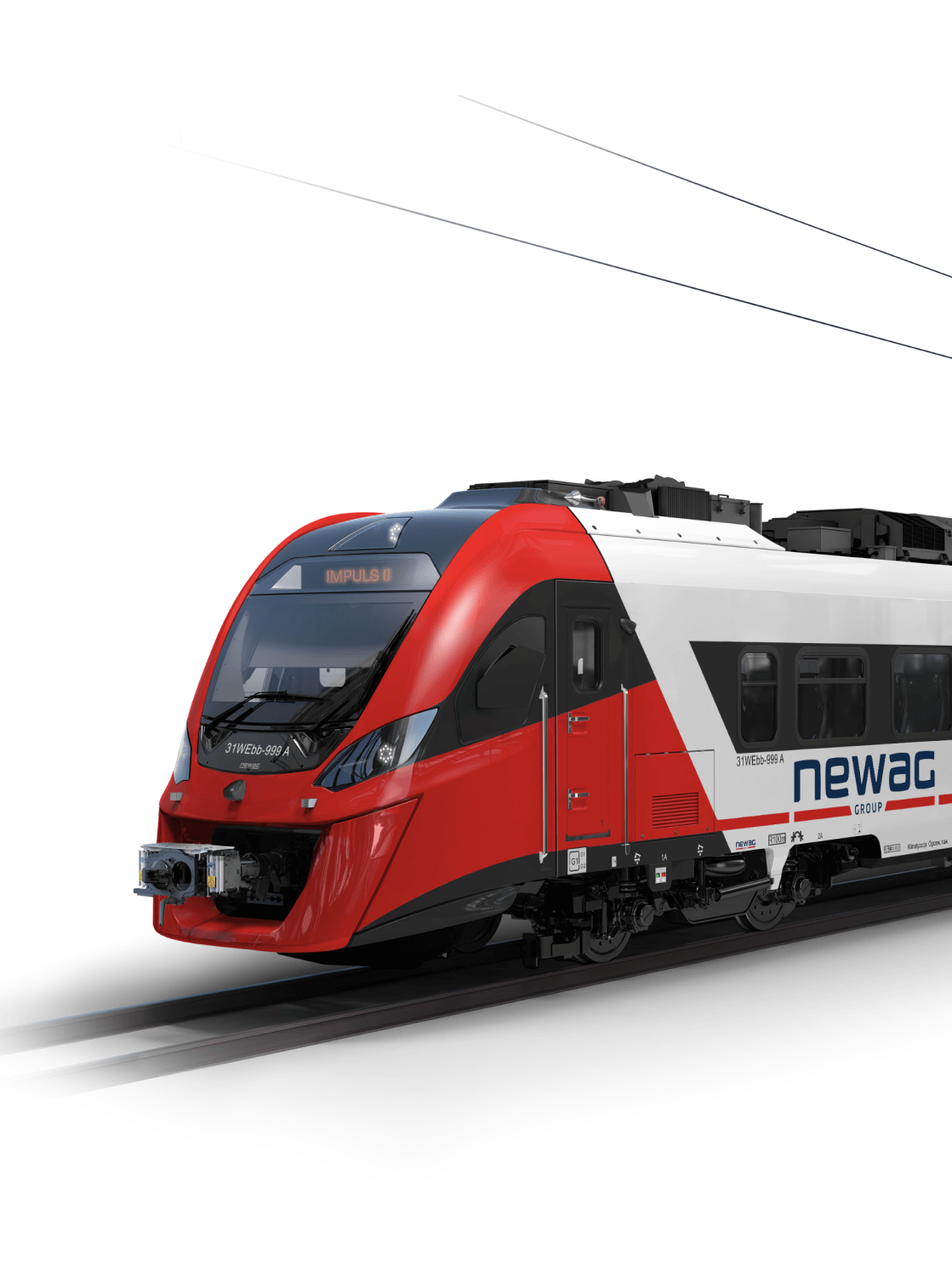
Platforma Impuls
Elektryczne Zespoły Trakcyjne z rodziny Impuls to najnowocześniejsze pojazdy szynowe produkowane w Polsce.
Dowiedź się więcej
Lokomotywy elektryczne
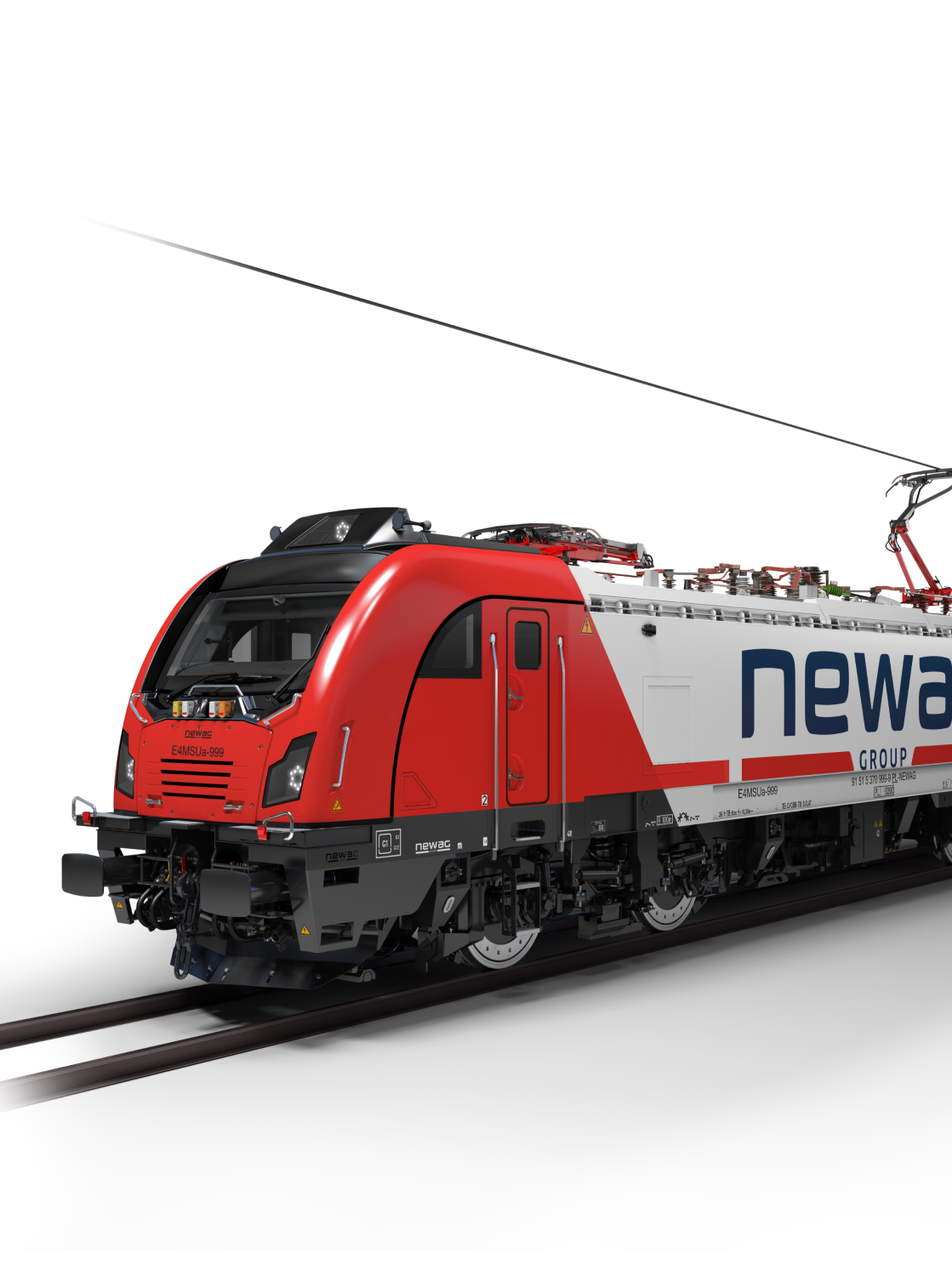
Lokomotywy elektryczne
W NEWAG S.A. skonstruowaliśmy nowoczesne lokomotywy elektryczne Griffin i Dragon.
Dowiedź się więcej
Lokomotywy spalinowe
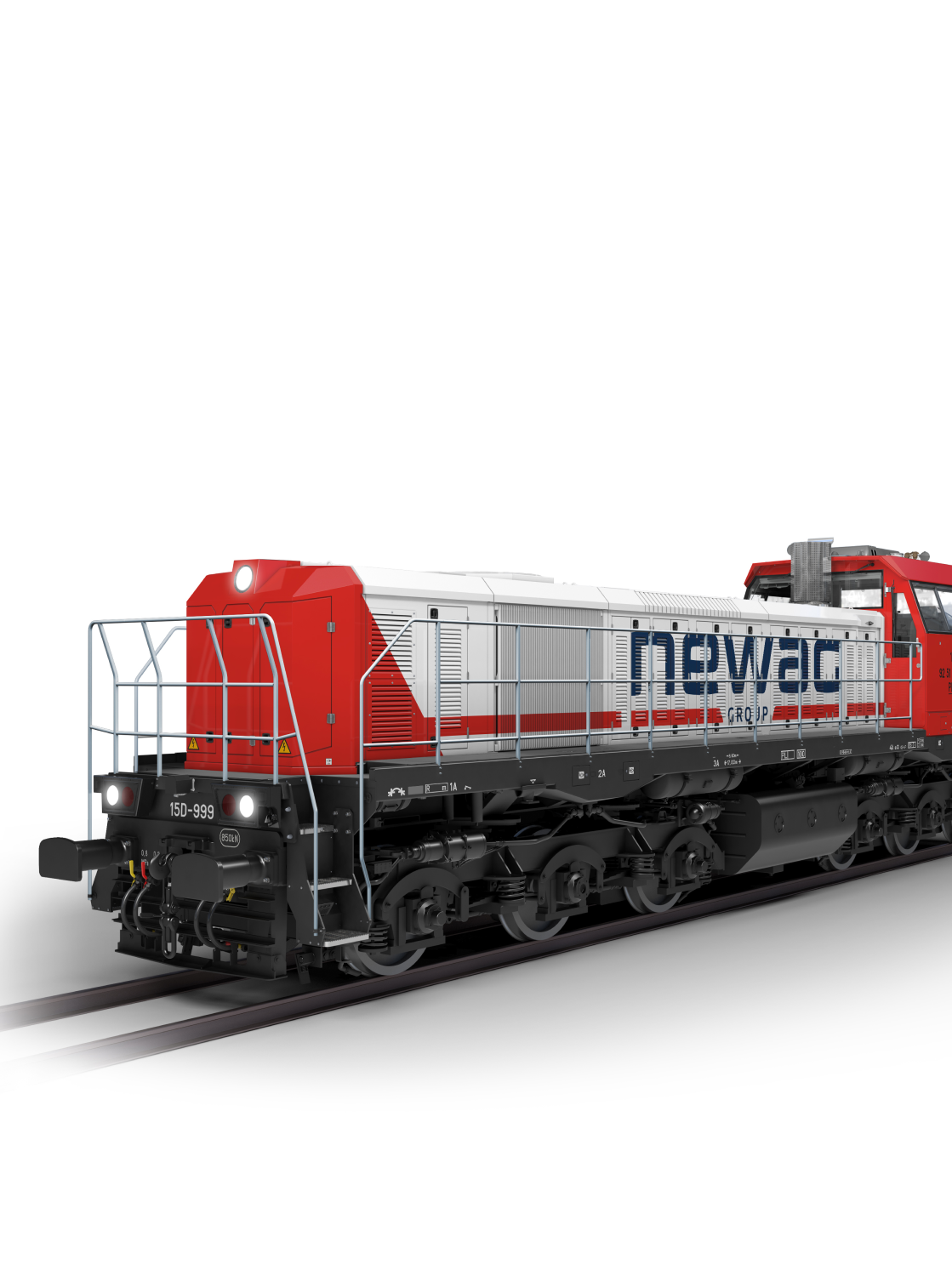
Lokomotywy spalinowe
W naszych zakładach prowadzimy kompletną modernizację lokomotyw spalinowych SM42 i SM48 do typu 18I, 6Dl,6Dg, 15/16D.
Dowiedź się więcej
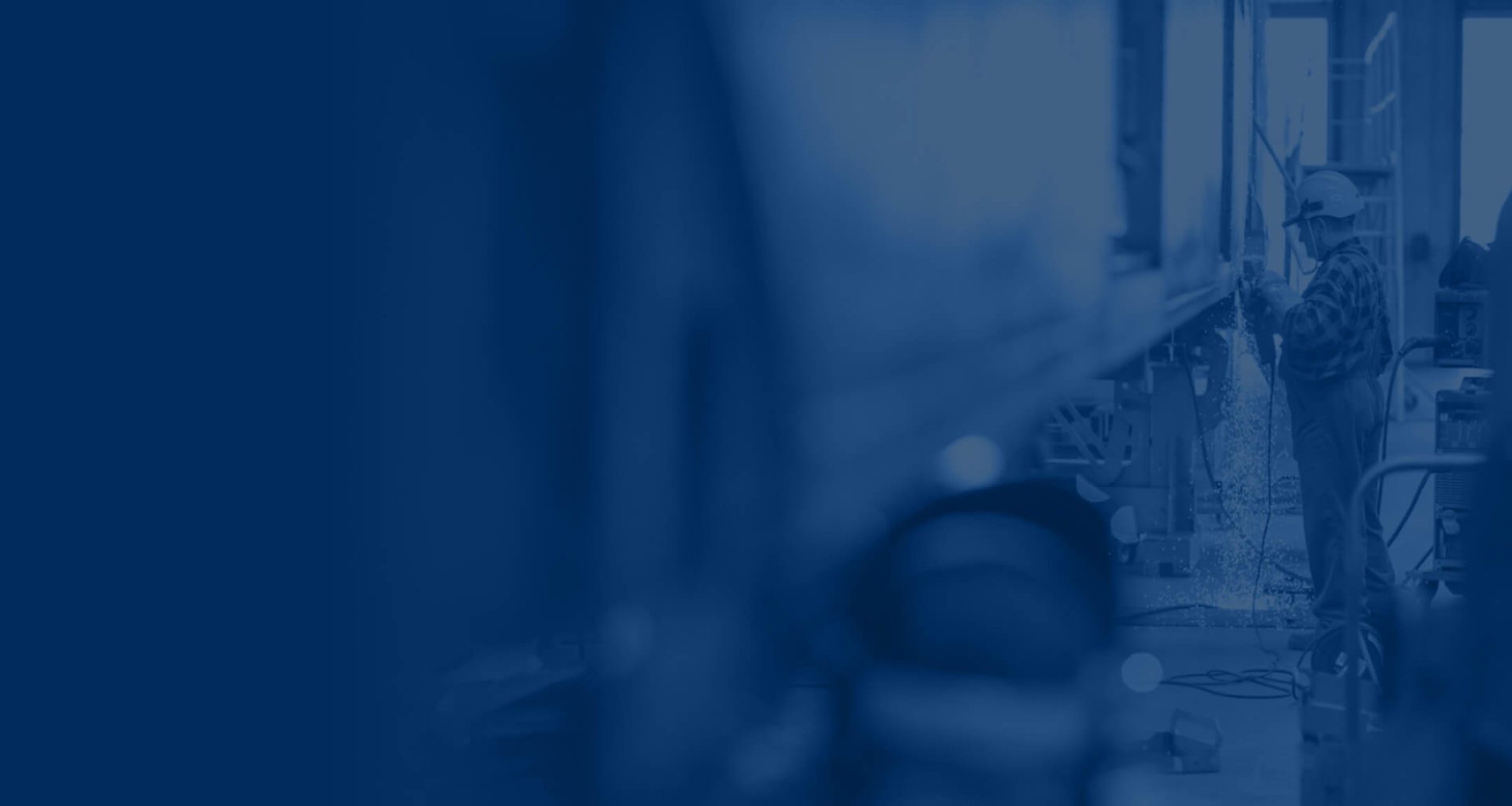
Kariera
Poszukujemy doświadczonych specjalistów, ale jesteśmy również otwarci na młode talenty, które dopiero rozpoczynają swoją karierę zawodową.
Nasz zespół to grupa profesjonalistów, nastawionych na rozwój zawodowy, którzy z pasją i zaangażowaniem tworzą innowacyjne produkty o najwyższej jakości.
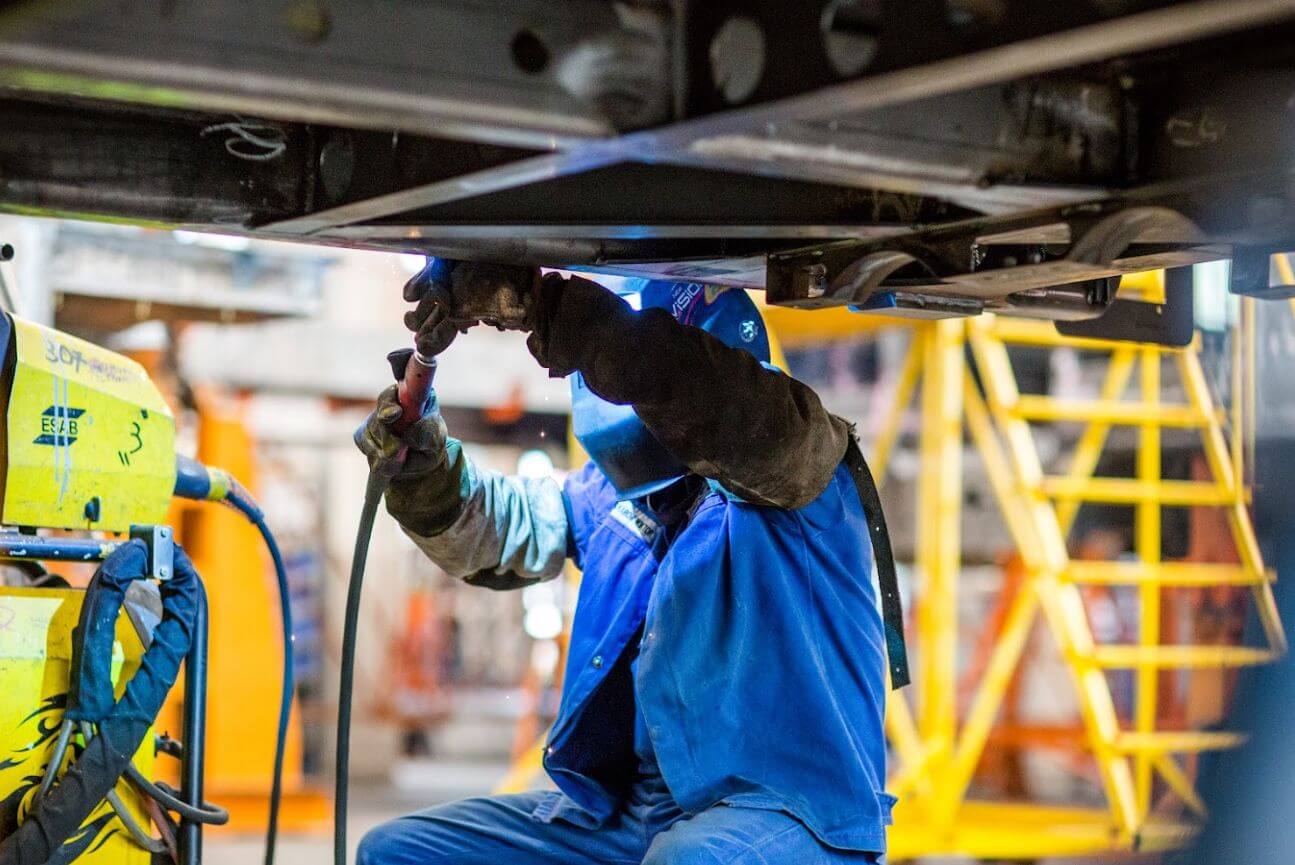
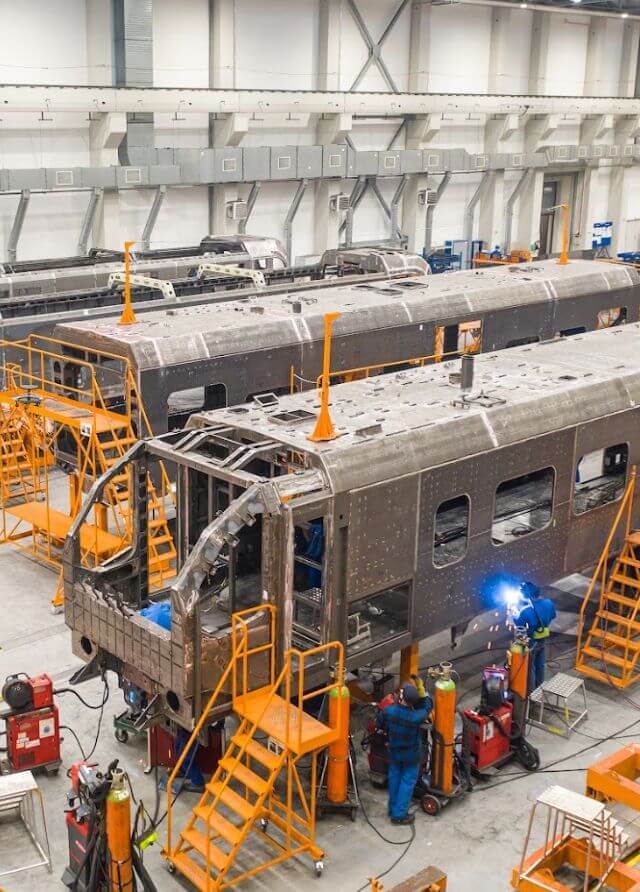
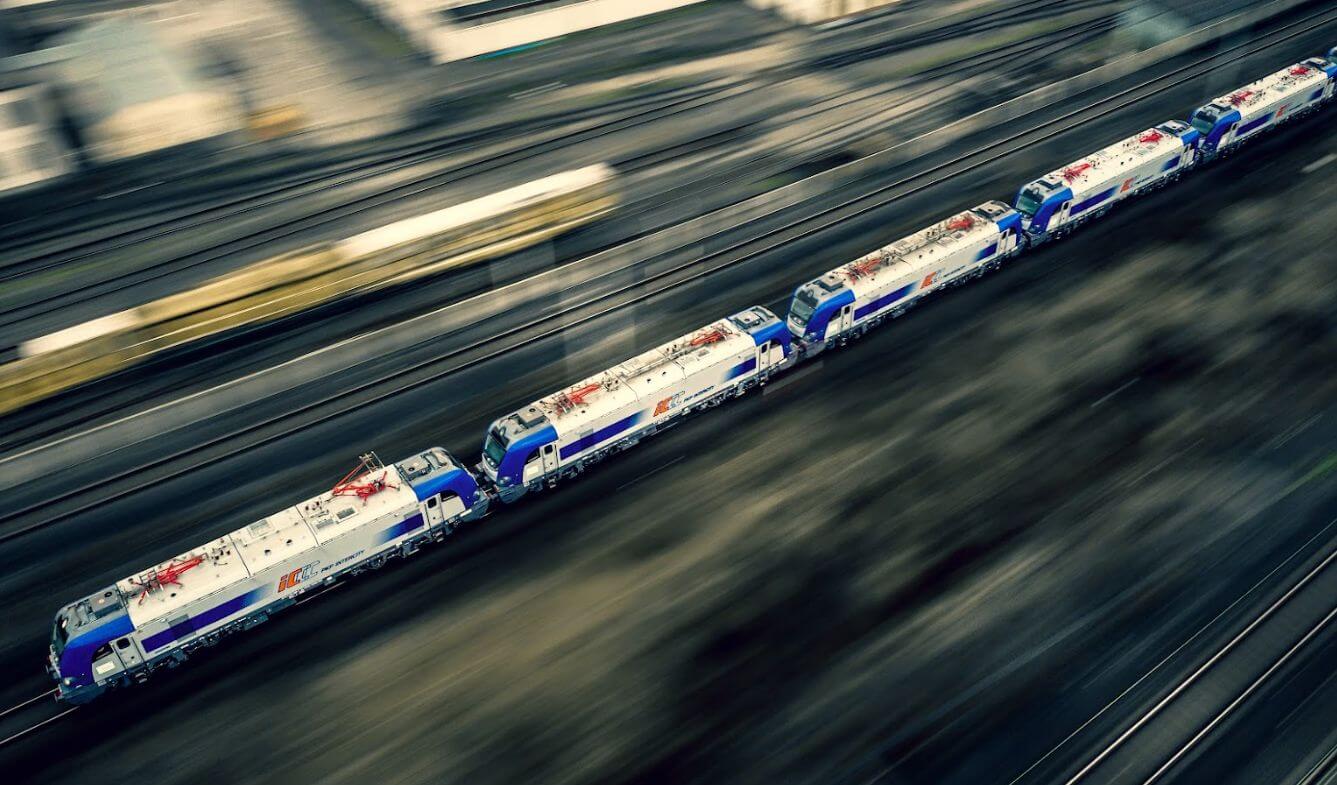
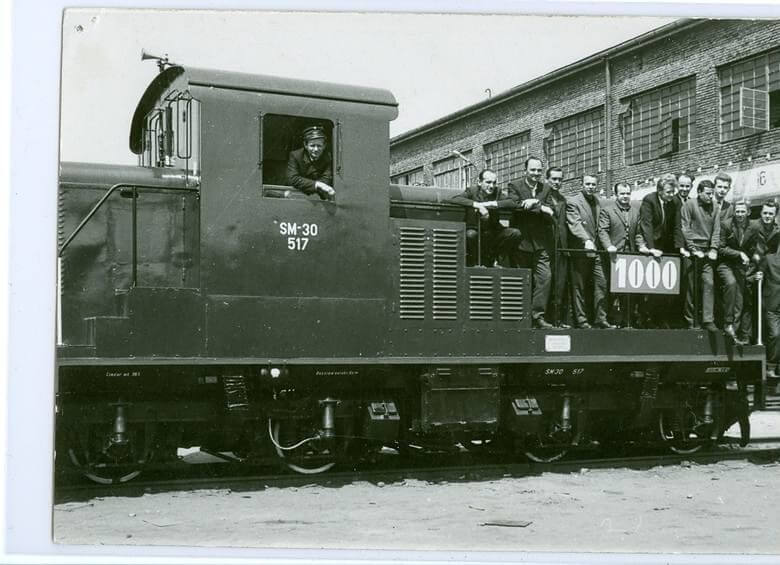
1876 — dla nowo wybudowanej kolei powstaje w Nowym Sączu zaplecze techniczno — remontowe o nazwie Cesarsko — Królewskie Warsztaty Kolei — dzisiejszy NEWAG.
Czytaj więcej
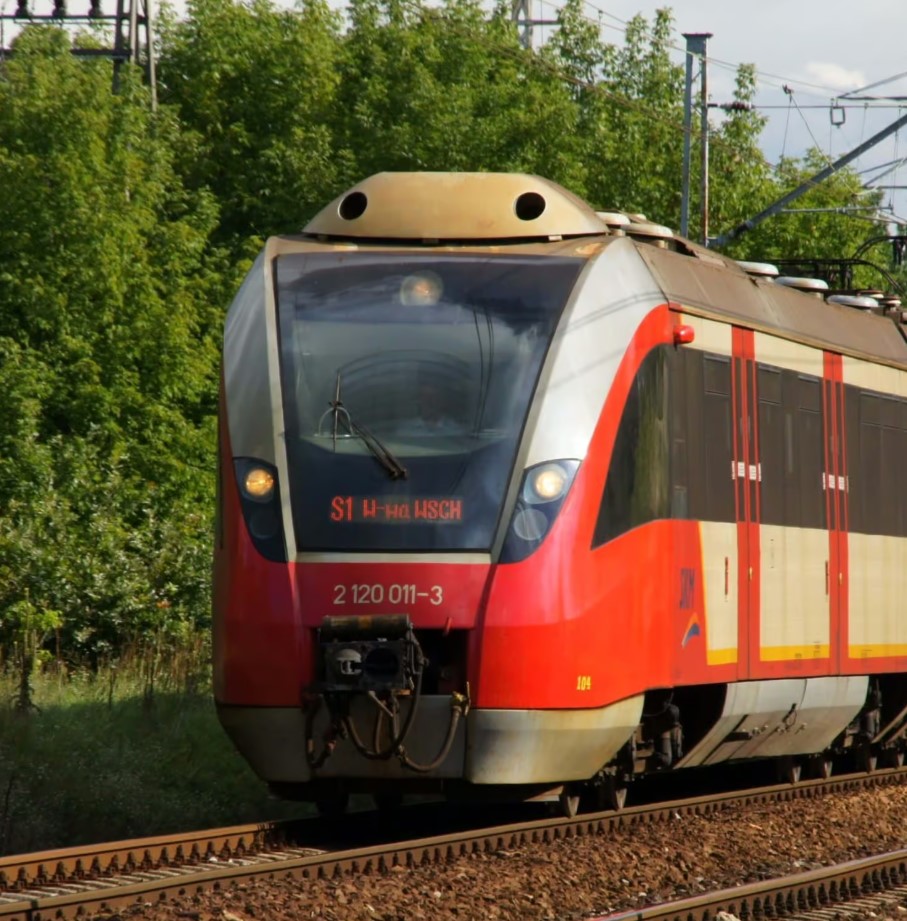
2005 – przekazanie do eksploatacji pierwszego naprawionego w Nowym Sączu elektrycznego zespołu trakcyjnego serii EN71.
Czytaj więcej
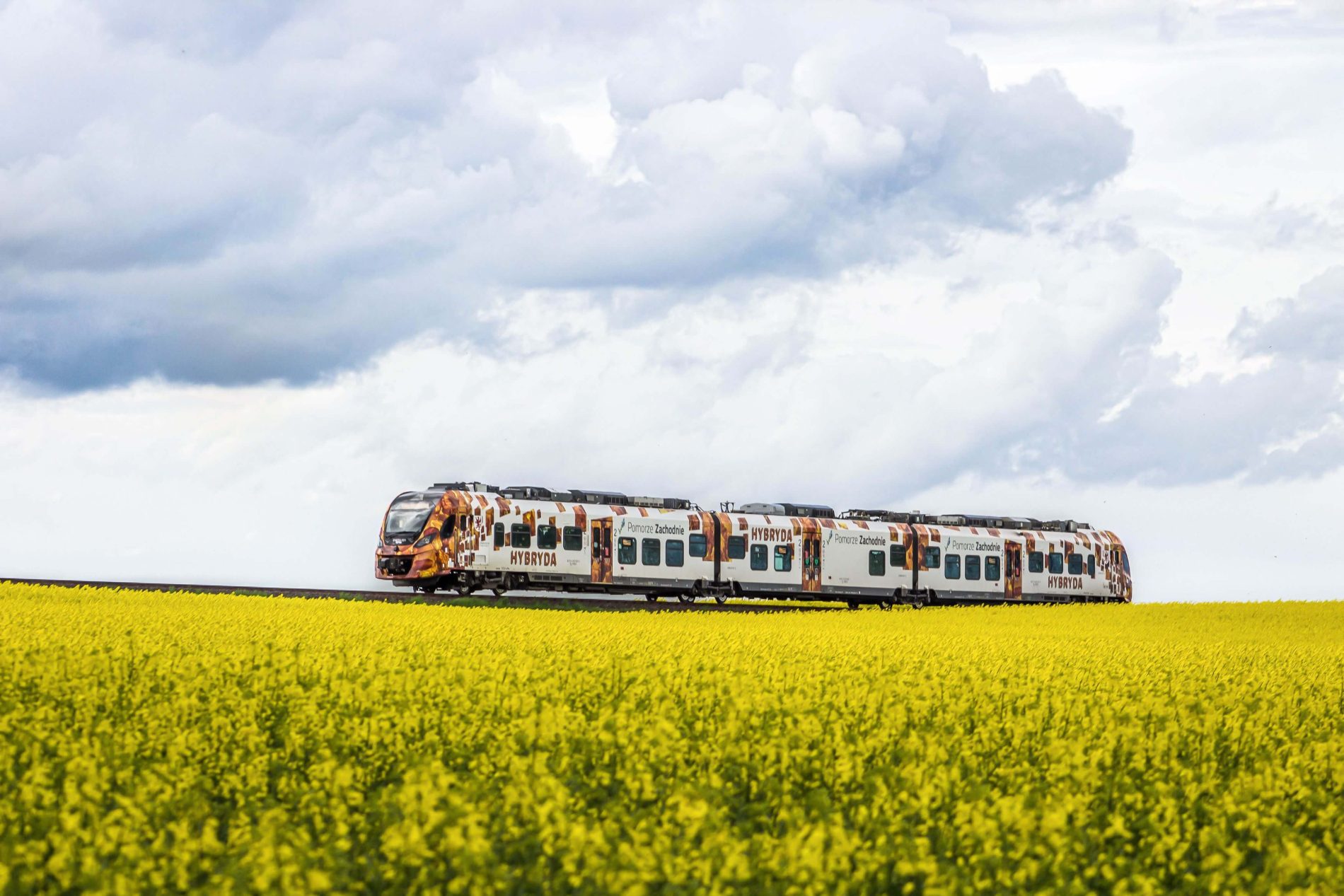
Nowy rekord Polski na torach. EZT IMPULS 45WE pojechał z prędkością 226 km/h. Impuls jest najszybszym pojazdem skonstruowanym i wyprodukowanym w Polsce.
Czytaj więcej